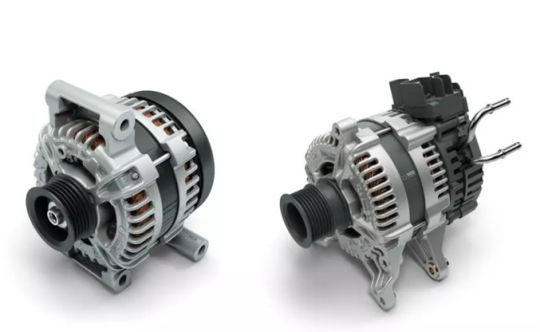
From the alternator to the Boost Recuperation Machine
In recent years, the alternator has developed from a simple component to a highly integrated boost recuperation machine (BRM). But what are the differences and what has remained the same?
When the three-phase generator, still colloquially known as the alternator, was only responsible for supplying energy to the vehicle and complex battery management systems were still a long way off, things were simple: If the charging indicator light flashed, either the V-belt had broken or the alternator had run out of coal. But a lot has happened in the meantime. However, much higher demands are placed on today's alternator: on the one hand, the electrical requirements for charging power have increased significantly, and on the other hand, the BRM is increasingly taking over the function of the starter in order to turn the classic combustion engine into a mild hybrid. In order to take these requirements into account, the classic charge controller was developed into a 48-volt inverter, which can now charge the lithium-ion battery. In order to effectively dissipate the resulting waste heat from the power electronics, in most applications the electronics are water-cooled and integrated into the engine's coolant circuit. On the belt side, the simple pulley suggests a “simple” belt, but in order to be able to transmit the drive power in hybrid operation, a ten-rib belt and two BRM near tensioning or deflection pulleys (decoupling tensioners) are necessary so that the belt has the highest possible enclosure the pulley has.
Electrical performance
Nowadays, conventional three-phase generators usually deliver between 90 and 140 amps. The larger the motor and the more powerful the electrical equipment, the more powerful the generator and battery have to be. Above 140 amps, however, the air becomes thin; only in the commercial vehicle sector are there individual models that deliver even more power - the cable cross-sections simply become too large. 140 amps at 14.3 charging voltage result in a total output of around 2 kW that such a generator can provide permanently - the efficiency is usually in the range of 67 percent, which means that around 3 kW of mechanical energy is required to produce 2 kW of electrical energy to generate – efficiency losses caused by the belt drive are ignored.
The Boost Recuperation Machine takes electrical performance to a whole new level: In addition to a comparable output power of 2.2 kW on the 12-volt rail, they also deliver up to 16 kW of power on the 48-volt rail into the on-board network when the vehicle is recuperating. The overall efficiency is also significantly higher: at 87 percent, around 20 percent more energy is converted into electrical power than is the case with a conventional three-phase generator. In addition to an optimized winding and a rotor reinforced with neodymium magnets, this saving is made possible by the electronic inverter, which can always operate the generator at its best. For this purpose, the BRM has a position sensor similar to the crankshaft sensor, so that the electronics always know how the rotor is positioned and its exact speed in order to be able to control recuperation and boost as effectively as possible.
The inverter is no longer just a passive circuit, but rather its own, highly developed controller that, depending on the vehicle manufacturer and model, is programmed with a specific charging/boost curve that is optimally tailored to the engine. A lot of effort that is worth it for manufacturers and drivers: In real operation, a mild hybrid saves an average of around 0.2 liters of fuel per 100 kilometres; for the manufacturer, this means a saving of 1.4 grams of CO² in fleet consumption.
What only seems to bring advantages in normal driving operations also offers a number of disadvantages in everyday workshop life: the belt drive with the decoupling tensioner is designed to be more complex, and the integration into the cooling water circuit turns what was previously a “quick change of thealternator” into a medium-sized operation including bleeding of the coolant circuit. And: Unlike the alternator, the BRM can no longer be repaired much. The coals can still be replaced – that’s it! The ball bearings could theoretically be replaced, but the position sensor, which is trained to the position of the rotor with millimetre precision, is in the way. Once removed, the inverter's software must be recalibrated, which cannot be done with the workshop diagnosis, but only with the manufacturer's tools. At the same time, the 48 V Li-ion battery and the DC/DC inverter add additional expensive components to the vehicle, which offer additional potential for errors. But no one expected that such a highly developed product would not be cheaper than its simpler predecessor, right?
Technical information provided by:
Stremtec BV Netherlands
www.stremtec.com